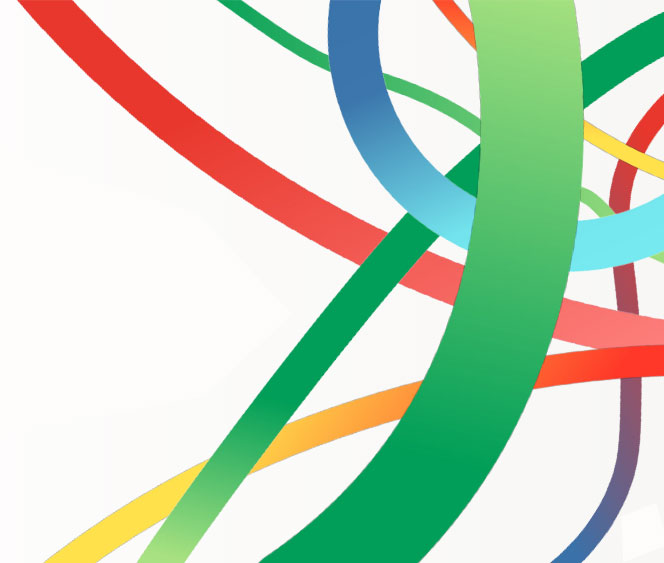
Nonwoven companies have been early movers in exploring the potential of post-consumer clothing waste, ahead of the European Union’s ban on the landfilling or incineration of it beginning in January 2025, and the imposition of an extended producer responsibility (EPR) scheme on brands to pay for the collection and disposal.
The European Commission’s Strategy for Textiles is further calling for all textile products on the EU market to be durable, repairable or recyclable – and largely made of recycled fibres – by 2030.
Nonwovens from regenerated mill waste fibres
The nonwovens industry already turns a lot of textile waste which has been mechanically recycled into second life products such as insulation for the automotive and construction industries, industrial wipes, mattress covers, padding etc., but to date this has been largely from regenerated mill waste fibres.
Mill waste fibres are comparatively pure compared to post-consumer apparel waste, where many finished articles are often based on blended fibres – most commonly of polyester and cotton – with elastanes, chemical finishes and many other impurities such as buttons, zips and linings to be removed before a bale of fibres can be shipped for reprocessing.
As a consequence, today’s mill waste is going to be much more valuable going forward, as the apparel brands look for recycled feedstocks that can be incorporated into their clothing ranges that are produced by the conventional route of yarn spinning, followed by weaving or knitting.
The successful spinning and further processing of recycled fibres in conventional textile processing is very much dependent on their purity and length, and short fibres are always problematic. Bales of virgin cotton, for example, have an average short-fibre content of 24.6%, but short-fibre content in recycled yarn waste from mills is on average 46.9%, which already makes turning it into new yarns for spinning challenging.
Post-consumer waste, however, will have a much higher percentage of short fibres, amplifying the problem.
At best, it is estimated that textile apparel containing 40% post-consumer waste fibres is the current limit to be achieved in blends with virgin fibres for spinning.
French EPR scheme experience
An example of where this is likely to lead is already to be found in France, where an EPR scheme for the collection and recycling of textile waste has been in operation since 2008.
In its latest-available figures, Paris-based Refashion, the non-profit association formed to administer the French EPR scheme, oversaw the collection of 260,000 tons of consumer textile waste in 2022, representing a collection success rate of 31% against set targets. The waste that was then subsequently sorted by 67 contracted sorting facilities amounted to 188,000 tons, representing a 23% success rate.
Of this sorted waste, 59.5% – roughly 112,000 tons – was resold or reused and a further 31.3%, or 59,000 tons, was given a second life in nonwoven products, with only a small percentage unravelled and turned into new yarns for spinners. So there is still a long way to go.
Ecomodulation bonus already applicable to certain nonwoven applications
A notable further development of the French EPR scheme has been the recent introduction of ‘ecomodulation’ fees which are bonuses for manufacturers who are able to demonstrate either the durability of their products, provide environmental certifications or incorporate recycled materials into their collections. Some €237 million has been allocated to this scheme for the 2023-28 period, which should prove a major incentive for further change.
Specifically, products incorporating raw materials from the recycling of post-consumer textile waste will qualify for a bonus of €1,000 per ton, and those made from recycled mill waste a bonus of €500 per ton – significant concessions when considering the huge volumes that can be involved.
If such a scheme were to be extended Europe-wide, it’s likely that much available mill waste would be snapped up by the apparel brands for incorporation into their vast ranges, that could then benefit for the lower ecomodulation bonus. This is already happening in France.
To qualify for the higher ecomodulation bonus, however, nonwovens definitely hold all the cards.
“The nonwovens industry should be proud of the applications for recycled fibres it has already developed,” said Charles Junker, head of sales for Andritz Laroche. “Even with the latest fibre-to-fibre chemical recycling methods being commercialised, only 30-40% of recycled content can be incorporated into yarns for conventional spinning and we are already achieving 100% in many high-value nonwoven products.”
Challenge in sorting
Charles Junker was speaking during a recent webtalk organised by the textile machinery branch of Germany’s VDMA on the subject of automated sorting, which has been identified as something of a bottleneck in growing the European textile recycling industry at present.
The Gold Standard for mechanical recycling is currently without doubt Nouvelles Fibres Textiles, based in Amplepuis, France, which Andritz has established in partnership with textile manufacturer Les Tissages de Charlieu, sorting company Synergies TLC and sensor specialist Pellenc. It was inaugurated in November last year.
Charles Junker observed that the challenge in sorting is to be able to automatically and rapidly classify garments in order to maximise the value of the fibres they contain.
Refining the textile waste
The Nouvelles Fibres Textiles system employs processes for consistently refining the textile waste, starting with a sorting line for full waste garments, a second for cutting and secondary sorting and then on to a cleaning and tearing line.
Charles Junker provided an example of how the system handles a bale of cotton and polycotton denim waste.
After garment spreading to avoid overlapping, the system can be initially set to separate all cotton items that are more than 90% blue in colour from the rest, removing all non-cotton and other coloured items and producing a second bale.
This is then cut into clips and fed through the second line to remove everything remaining that is not cotton or blue, such as pocket linings. It is then baled again.
The cleaning and tearing line then removes all other remaining impurities to result in a bale of 98-99% clean fibre. This is suitable for incorporation as a percentage of the feedstocks for yarn spinning, but can realistically be turned completely into new nonwovens.
Charles Junker said the Nouvelles Fibres Textiles will soon by at the stage of handling three tons of material an hour, and by the end of this year is targeting six tons an hour.
“Mechanical recycling is an immediate response but won’t be the only solution and we are also now working on the development of a refined system for the production of recycled yarns, and also on chemical recycling treatments,” he concluded.